Cold Heading: A Comprehensive Guide
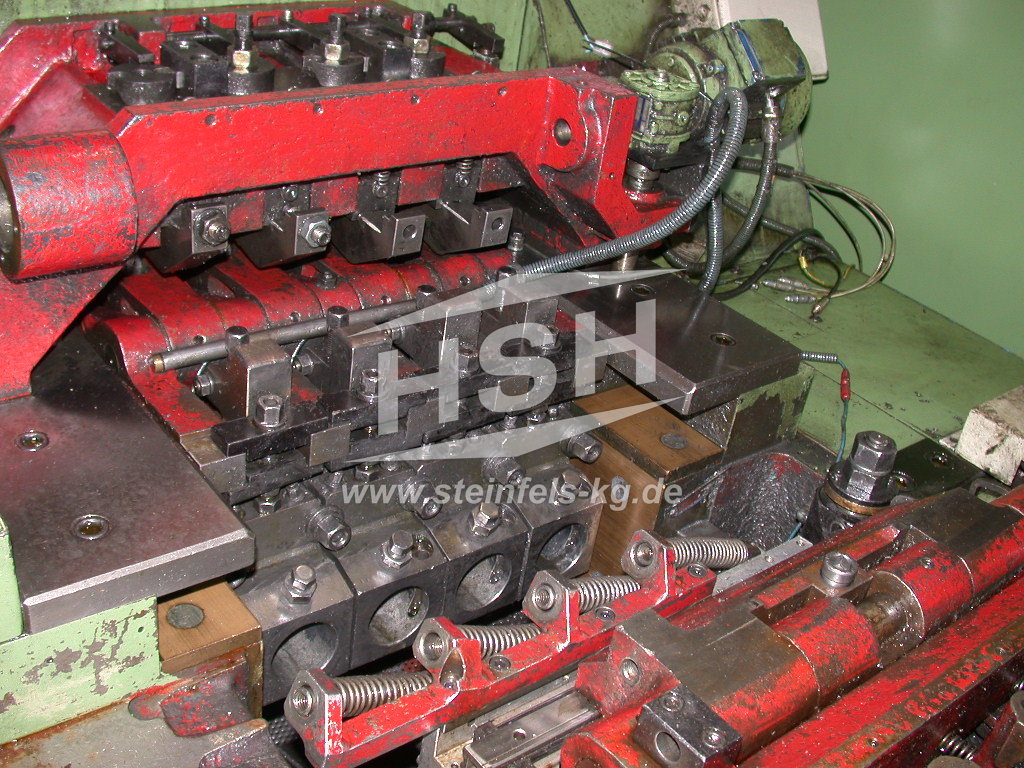
Definition and Basic Principles of Cold Heading
Cold heading is the process of progressively forming a specified shape from metal wire without adding heat. This is achieved using a series of dies, hammers, and punches at high speed. In simple terms, wire is fed into a machine, cut into pieces, and formed into the desired shape at room temperature. This method is highly efficient and cost-effective for manufacturing large quantities.
The Crucial Role in Precision Manufacturing of Small Parts
It plays a critical role in the manufacturing of small parts like fasteners, screws, bolts, and other essential components used across various industries. This process allows for the rapid production of these parts with high precision and consistency, which is crucial in sectors such as automotive, aerospace, electronics, and construction. Cold heading not only ensures that these parts meet strict strength and dimensional tolerances but also significantly reduces material waste, making it a more cost-effective and sustainable solution compared to traditional machining.
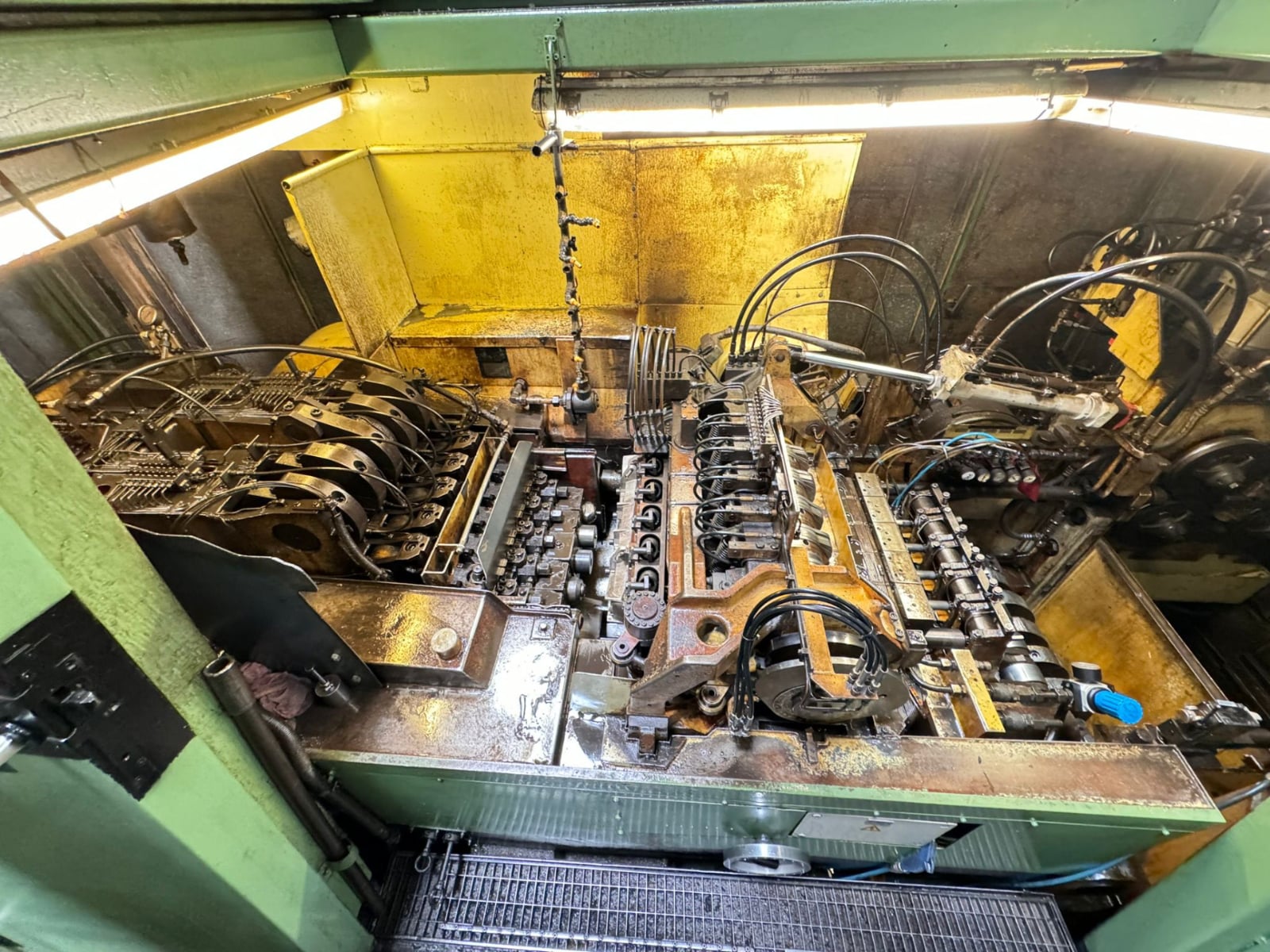
Advantages of Cold Heading
One of the primary benefits is its efficiency; the process allows for the mass production of components at high speeds, reducing lead times significantly compared to traditional machining methods. Additionally, cold heading minimizes material waste, as the metal is formed rather than cut, leading to cost savings on raw materials.
The process also enhances the strength of the parts due to the cold working of the material, resulting in a finer grain structure. Furthermore, cold heading provides excellent precision and repeatability, making it ideal for producing complex shapes with tight tolerances.
Here you will find all the advantages of cold heading listed:
- High Precision: Achieves tight tolerances.
- Fast Production Rates: High-speed manufacturing.
- Large Volume Capacity: Suitable for high-volume production.
- Reduced Material Waste: Minimizes raw material waste.
- Improved Physical Properties: Enhances material properties through the forming process.
- Cost Reduction Compared to Machining: Lower costs compared to machining operations.
- Wide Range of Diameters: Capable of producing a broad range of diameters.
- Custom Configurations: Tailored to customer specifications.
- Secondary Operations: Additional processing steps to complete fully customized parts.
Basic Cold Heading Techniques
Upsetting
A portion of a metal blank or wire is compressed during upsetting to increase its diameter without changing the overall length. By applying high pressure to the material at room temperature, upsetting reshapes the metal efficiently, ensuring that the structure remains strong and uniform. This technique is highly valued for its ability to produce high volumes of parts with minimal material waste while maintaining precise dimensions.
This method is primarily used to create heads on fasteners like bolts and screws, where the head needs to be larger than the shaft.
Extrusions
This is a cold heading technique that involves forcing metal through a die to create elongated shapes with a consistent cross-section. The process allows for intricate shapes and designs that maintain structural integrity, as the metal is cold worked without cutting or removing material. Extrusions in cold heading are highly efficient, producing strong, durable parts with minimal waste.
In cold heading, extrusion can be used to form components like shafts, pins, and other cylindrical parts where length and precision are essential.
Materials
Cold heading typically uses materials like steel, aluminum, copper alloys, and stainless steel. These materials are chosen for their malleability and strength, which are crucial for withstanding the high-pressure deformation involved in the cold heading process.
Steel, especially carbon and alloy steel, is favored due to its excellent strength and durability, making it ideal for automotive and construction components.
Aluminum is preferred for lightweight applications, offering a good balance of strength and corrosion resistance.
Copper alloys are used when electrical conductivity or corrosion resistance is essential, making them ideal for electrical components.
Stainless steel is often chosen for its corrosion resistance and strength, particularly in environments where durability and longevity are critical.
Are you interested in manufacturing screws?
Discover our machines for screw production that are available for sale.
Step-by-Step Tutorial: The Cold Heading Process
1. Material Selection and Preparation
Select Material: Typically, wire rods or metal blanks made from steel, aluminum, copper alloys, or stainless steel are used. The choice depends on the required properties of the final product, such as strength, corrosion resistance, or conductivity.
Wire Preparation: The metal wire is usually lubricated to reduce friction during the cold heading process and prevent tool wear.
Coiling: The wire is coiled and placed into a feeder system, ready to be straightened and fed into the machine.
2. Feeding the Metal
Straightening: The coiled wire is straightened as it is fed into the machine to ensure accuracy and consistency in the forming process.
Cutting to Length: The machine cuts the wire into specific lengths, which will become the individual parts. This step is automated for precision and efficiency.
Positioning: The cut metal piece is positioned in front of the cold heading dies, ready for the forming process to begin.
3. Shape the metal through high-pressure deformation
Die Setup: Cold heading machines use a series of dies to form the metal. These dies are custom-designed to produce the desired shape of the final product.
High-Pressure Deformation: The metal blank is struck by a punch that forces it into the die cavity. This process deforms the metal at room temperature, creating the desired shape without removing material.
Multiple Operations: Depending on the complexity of the part, the metal may pass through several different dies, each one progressively shaping the part closer to the final form.
4. Complete complex shaping
Progressive Forming: For parts that require complex shapes or precise features, the cold heading process may involve multiple stages. Each stage further refines the shape by compressing, extruding, or upsetting different sections of the part.
Secondary Operations: Complex fasteners and components often require secondary operations that cannot be performed on a cold heading machine. These include:
- Thread rolling
- Drilling and tapping
- Knurling and grooving
- Stamping
- Heat treating
- Plating
- Grinding and shaving
- Metal finishing and polishing
- CNC milling
- Flattening
- Piercing
Quality Control: Each stage is monitored for precision and quality. Sensors and automated controls ensure that the parts meet exact tolerances.
5. Final Inspection and Finishing
Inspection: Finished parts are inspected for defects, dimensional accuracy, and overall quality. Modern cold heading machines often include sensors and quality control systems that perform this check automatically.
Finishing: If needed, the parts may undergo finishing processes like heat treatment to enhance their strength, coating for corrosion resistance, or surface finishing to improve aesthetics.
Packaging: Once inspected and approved, the parts are packaged for distribution to manufacturers, suppliers, or end-users, depending on the production chain and final application.
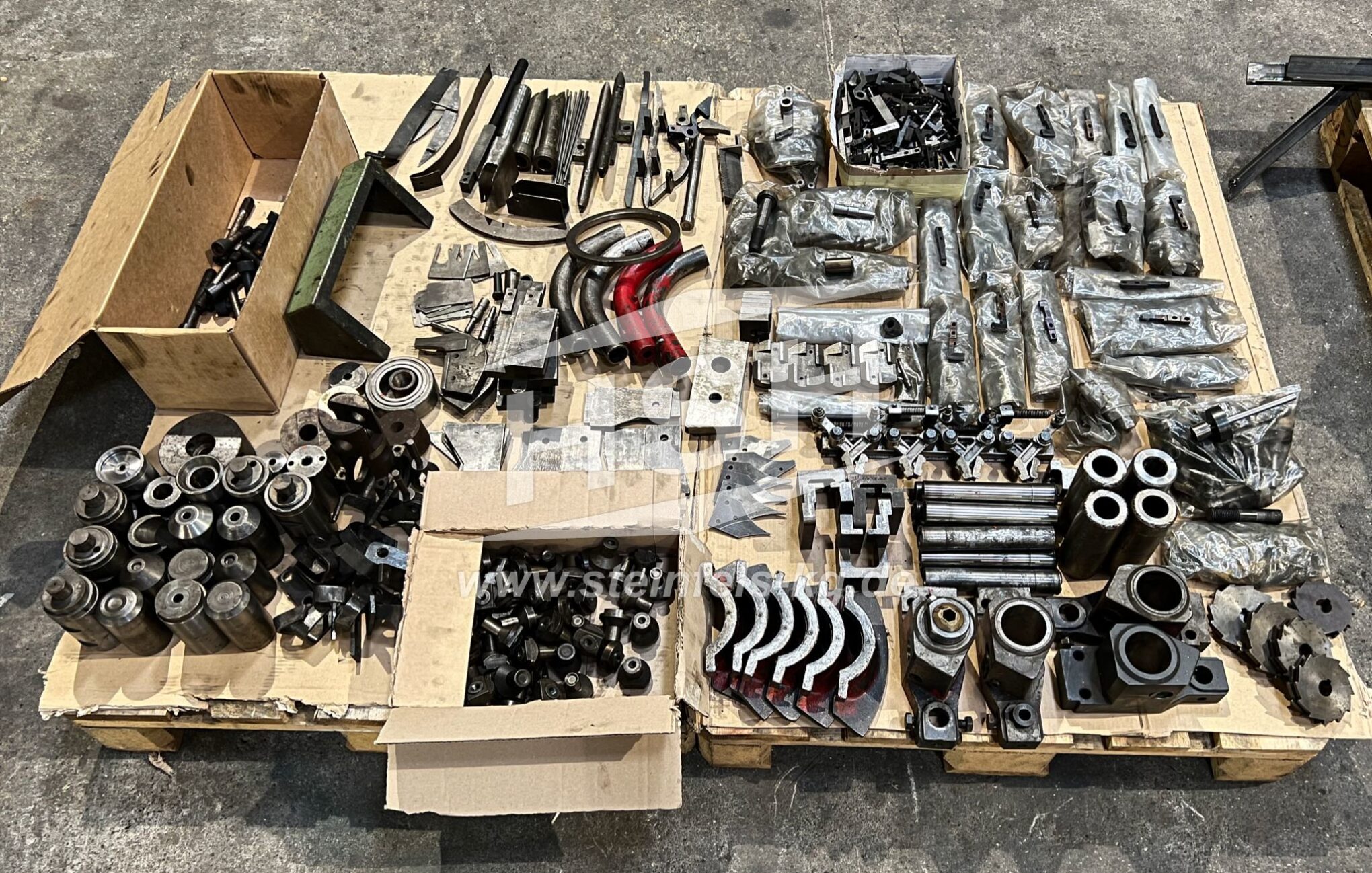
Applications of Cold Heading
Cold heading was originally developed for making fasteners but has since become a versatile manufacturing process. It’s now used to produce a wide range of parts and components found in countless products and structures worldwide. This technique is crucial in industries like automotive, aerospace, electronics, and construction. In the automotive sector, cold heading creates high-strength parts like engine components and drive shafts. In electronics, it’s used for connectors, pins, and micro-components that need precise tolerances.
Advancements in cold heading technology, such as improved dies and automation, have expanded its capabilities. This has enabled the production of more complex and intricate parts. New applications include the medical field, where cold heading is used to make surgical instruments and implants that require high precision.
Cold heading is also known for its cost-effectiveness and sustainability. It reduces material waste and minimizes the need for secondary machining. This leads to significant cost savings and supports high production volumes. As industries look for more efficient and eco-friendly manufacturing methods, cold heading continues to grow in importance.
Cold Heading vs. Other Manufacturing Processes
1. Machining
Material Waste: Cold heading significantly reduces material waste compared to machining. Machining typically involves cutting away material from a workpiece, which results in a substantial amount of scrap. In contrast, cold heading forms parts by deforming metal, preserving almost all of the material.
Production Speed: Cold heading is much faster than machining for high-volume production. Once the setup is complete, parts can be produced rapidly and with high repeatability, making it ideal for mass production.
Cost: Due to less material waste and faster production times, cold heading generally offers lower per-unit costs, especially in large quantities. However, the initial tooling costs for cold heading can be higher.
2. Hot Forging
Temperature: Cold heading is performed at room temperature, whereas hot forging requires heating the material to high temperatures. This makes cold heading more energy-efficient and suitable for materials that can be formed without the need for heating.
Part Strength: Cold heading typically results in stronger parts because the material is work-hardened during the process. Hot forging can also produce strong parts but may require additional steps like heat treatment to achieve similar strength.
Surface Finish: Cold heading generally produces a better surface finish compared to hot forging, which often requires additional finishing processes to achieve the desired surface quality.
3. Stamping
Complexity: While both cold heading and stamping can produce parts quickly, cold heading is better suited for creating three-dimensional shapes, especially those with varying thicknesses or complex geometries. Stamping is typically used for flat parts or those with less dimensional depth.
Material Thickness: Cold heading is ideal for thicker parts that require significant deformation, whereas stamping is often limited to thinner materials.
Tooling: Both processes require precise tooling, but cold heading tooling is typically more robust to withstand the high pressures involved in forming thicker parts.
4. Casting
Material Use: Cold heading is more efficient in material use compared to casting, where some material is often lost in the form of excess or unusable metal. Casting involves pouring molten metal into a mold, which can result in more waste and less material conservation.
Strength and Durability: Cold-headed parts often have superior strength and durability due to the work-hardening effect, while cast parts may require additional treatments to achieve similar properties.
Production Time: Cold heading offers faster production times for high volumes, as it eliminates the need for cooling and solidification phases required in casting.
Challenges
While cold heading is a highly efficient and cost-effective manufacturing process, it does come with its own set of challenges. One of the primary difficulties is the initial cost of tooling and machine setup. The dies and punches used in this process must be custom-designed and manufactured to precise specifications, which can be expensive, especially for small production runs or complex parts.
Another challenge is the material limitations. Not all metals are suitable for cold heading. The process works best with materials that have good ductility and can withstand high levels of deformation without cracking. Certain hard or brittle metals may require special treatment or might not be suitable at all, limiting the range of materials that can be used.
Maintaining the precision and quality of parts over long production runs can also be challenging. The high pressures involved in cold heading can lead to tool wear, which can affect the accuracy of the parts produced. Regular maintenance and monitoring are required to ensure consistent quality, adding to the operational costs.
Furthermore, cold heading is generally more suited to high-volume production due to the significant upfront costs of tooling and setup. This can make it less economical for smaller batches or highly customized orders. The process is also less flexible when it comes to making design changes, as any modification typically requires new tooling, leading to additional costs and time delays.
Lastly, the complexity of cold heading operations requires skilled operators and engineers who can design, maintain, and troubleshoot the machinery and processes. Finding and training personnel with the necessary expertise can be a challenge for manufacturers.
Overall, while cold heading offers many benefits, overcoming these challenges is essential to fully leverage its potential in modern manufacturing.
Sustainability
Cold heading is a sustainable manufacturing process, offering several environmental benefits. One of its main advantages is the reduction of material waste. Unlike machining, which cuts away large portions of metal, this method forms parts by deforming the material, preserving almost all of it. This leads to significantly less scrap.
The process also requires less energy because it operates at room temperature. This contrasts with hot forging or casting, which need high temperatures and thus consume more energy. As a result, the overall carbon footprint is smaller, helping reduce greenhouse gas emissions.
Additionally, this technique often eliminates the need for secondary machining or finishing. This further reduces energy consumption and material waste. The parts produced are strong and durable, requiring less maintenance or replacement, which extends their lifecycle.
As industries focus more on sustainability, this method stands out as an eco-friendly choice. It supports efficient production while meeting the demand for environmentally conscious manufacturing practices.
Are you interested in manufacturing screws?
Discover our machines for screw production that are available for sale.
The Role of Technology in Cold Heading
Technology has significantly enhanced the efficiency, precision, and adaptability of this metal forming process. Modern machines now feature advanced automation systems, including robotics and CNC technology. These systems allow for high-speed production with minimal human intervention, ensuring consistent quality and faster turnaround times.
Real-time monitoring and sensor technology have transformed quality control. These tools detect and correct issues during production, ensuring each part meets exact specifications. This level of precision is crucial in industries like automotive and aerospace, where even small defects can cause major problems.
Advancements in die materials and coatings have also improved the durability of tooling. High-performance alloys and coatings help dies withstand the extreme pressures of the process, reducing downtime and maintenance costs.
Technology has also broadened the range of materials and complex shapes that can be handled. Sophisticated design software enables engineers to create and simulate intricate part designs before production begins. This capability has opened up new applications in fields such as medical devices and electronics.
What to Expect in the Future
The future of cold heading looks promising, with advancements in technology and materials poised to expand its capabilities even further. As industries continue to demand faster, more cost-effective, and sustainable manufacturing processes, it is expected to play an increasingly vital role. Here are some key trends and developments to watch:
Increased Automation and Precision: With the integration of advanced automation, including robotics and AI-driven controls, cold heading machines will become even more precise and efficient. This will allow for the production of more complex and intricate parts at higher speeds, reducing lead times and costs.
New Material Applications: As material science progresses, expect to see cold heading applied to a broader range of metals and alloys, including those that are currently challenging to form at room temperature. This will open up new opportunities in industries like aerospace, medical devices, and high-performance electronics.
Enhanced Sustainability: The push for greener manufacturing practices will drive innovations in cold heading, making it even more energy-efficient and reducing its environmental impact. Advances in lubrication technologies, die materials, and energy recovery systems could further reduce the process’s carbon footprint.
Customization and Flexibility: Future cold heading processes will likely become more adaptable, allowing for greater customization of parts without extensive retooling. This will make the process more accessible for smaller production runs and specialized applications.
Integration with Additive Manufacturing: As additive manufacturing (3D printing) becomes more prevalent, there may be synergies between cold heading and these technologies. Combining cold heading with additive processes could result in hybrid manufacturing techniques that leverage the strengths of both, creating new possibilities for complex part production.
Summary
The metal forming process discussed in this article has evolved significantly from its initial use in fastener production. It now plays a critical role in creating components for industries like automotive, aerospace, electronics, and construction. The process is known for its efficiency, producing high volumes of strong, precise parts with minimal material waste and lower costs.
In the future, advancements in technology will likely enhance this method even more. Automation, new materials, and a focus on sustainability will drive its growth. Combining it with other manufacturing techniques could unlock new possibilities.
In summary, this metal forming method is well-suited to meet the demands of today’s industries and is poised for a promising future in manufacturing.
Leading the Industry for 60 Years
For six decades, Helmut Steinfels GmbH & Co. KG has been a cornerstone in the global trade of second-hand machines for the wire and fastener industry. Our strong relationships with numerous machine producers and manufacturers, coupled with swift transactions between customers and suppliers, have cemented our position as a market leader.
Comprehensive Services for Buying and Selling Machinery
With an extensive inventory of machinery stored by us and our partners, HSH Steinfels is dedicated to helping you find the perfect equipment for your needs. If you’re looking to sell used machinery, we can either purchase it directly or connect you with the right buyer.